Powder coating is a popular method for applying a durable, protective finish to a wide range of products. By using finely ground particles of pigment and resin, which are electrostatically charged and sprayed onto a surface, this process makes a strong, even, and long-lasting coat. Whether coating metal furniture, automotive parts, or machinery, powder coating ensures that products are resistant to scratches, fading, and corrosion.
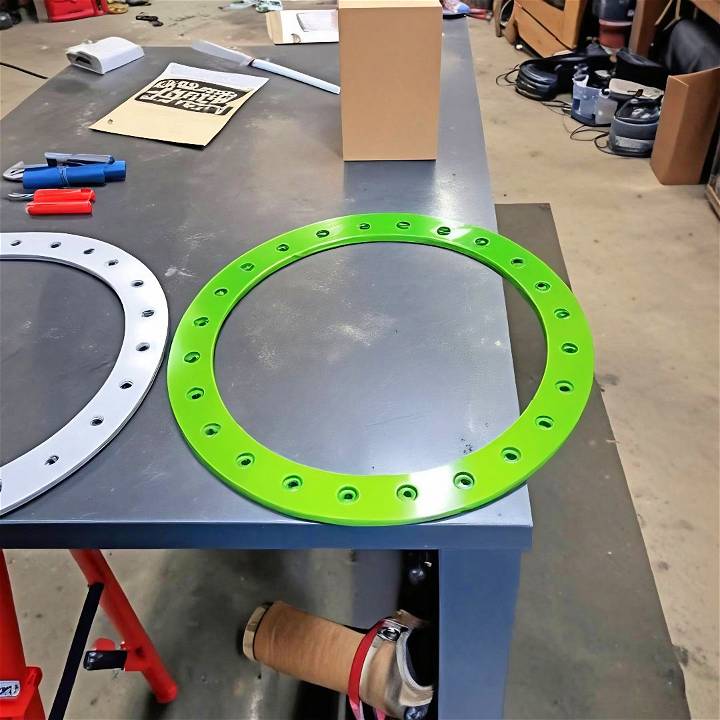
To achieve the best results, it’s important to follow specific steps. Learning how to powder coat starts with surface preparation, which can involve cleaning, degreasing, and sandblasting to make sure the surface is free of any contaminants. After preparation, the powder is applied, and the coated item is cured in an oven at high temperatures. This process produces a smooth, professional finish that stands the test of time.
What Exactly is Powder Coating?
Imagine a paint that, instead of being liquid, is in powder form. That’s essentially what powder coating is. It’s applied as a free-flowing, dry powder. The main difference between a conventional liquid paint and a powder coating is that the latter does not require a solvent to keep the binder and filler parts in a liquid suspension form. This dry powder is electrostatically charged and sprayed onto the surface to be coated. Then, it’s cured under heat to allow it to flow and form a “skin.” This skin is the coating.
The Benefits of Powder Coating
- Durability: Powder coating makes a thick, adhesive finish that lasts longer than traditional paint. It’s resistant to scratching, chipping, and fading.
- Variety: There’s a wide range of colors and finishes available, from smooth and glossy to textured.
- Eco-Friendly: Since there are no solvents, powder coating releases negligible amounts of VOCs (Volatile Organic Compounds), making it environmentally friendly.
- Cost-Effective: Powder coating is usually a one-coat finish, making the process quicker and more cost-effective than painting.
- Efficiency: The process has minimal wastage as overspray can be collected and reused.
How Does Powder Coating Work?
The process involves three key steps:
- Preparation: The surface to be coated is cleaned and prepped to ensure it’s free from oils, dirt, and rust.
- Application: The powder is electrostatically applied to the surface. The charged powder particles adhere to the electrically grounded surfaces until heated and fused into a smooth coating in the curing oven.
- Curing: The object enters a curing oven where, with the application of heat, the coating chemically reacts to produce long molecular chains, resulting in high cross-link density. This makes the finish particularly tough and resilient.
Is Powder Coating Right for Your Project?
Powder coating is ideal for items that require a durable and high-quality finish. It’s commonly used for automotive parts, outdoor furniture, home appliances, and much more. If you’re looking for a finish that is both protective and polished, powder coating might be the perfect solution.
Step by Step Instructions
Learn how to powder coat metal with our step-by-step guide, from gathering materials to curing and cooling for a perfect finish.
Step 1: Gather Your Materials
First off, let's break down everything you'll need:
- PCS 250 Dual Voltage Powder Coat Gun: Essential for applying powder.
- Powder Coating For Dummies Book: Because we all start somewhere.
- Powder Coat: I chose a vibrant green for my project.
- Powder Coating Accessory Kit: Includes air filters, safety lock wire, extra bottles, high temp tape, and silicone plugs.
- Air Dryer for Compressor: To keep humidity at bay, crucial for smooth application.
- Metal Cleaner: For prepping your items.
- A Suitable Oven: Can be a used one, just ensure it's large enough for your items.
These materials are crucial. The gun applies your powder, the air dryer keeps your air supply clean, and the oven cures the powder onto the metal. Each serves a specific role in ensuring a smooth, even coat.
Step 2: Prep Your Oven and Workspace
Make sure your oven works (mine did, phew!) and preheat it to 450* °F. While it's warming up, get your powder coating gear ready. A practice run on a smaller item, like a wrench, can be a great way to get a feel for the equipment.
Step 3: Prep Your Metal
Cleanliness is key. Use a quality cleaner to remove any grease, wax, or dirt from your items. I was powder coating bead lock rings, so ensuring they were impeccably clean was my first step.
Step 4: Set Up Your Powder Coating Gun
Assemble your PCS 250 or a similar powder coat gun and fill it with your chosen powder. Adjust the air pressure to around 10 PSI for a smooth flow of powder.
Step 5: Apply the Powder Coat
Make sure you have a good ground connection to your item. This is crucial for the powder to adhere correctly. Then, wearing appropriate PPE, apply an even coat of powder to the item. Go slow and steady to ensure full coverage.
Step 6: Cure Your Item
Once coated, place your item in the preheated oven. Let it sit at 450* °F until the powder flows out (it'll look shiny) and then lower the temperature to 400°F and bake for 20 minutes. This process cures the powder, making a hard, durable finish.
Step 7: Apply a Second Coat (Optional)
For a thicker, more vibrant finish, apply a second coat of powder and cure again. This can make a significant difference in the final appearance.
Step 8: Cool and Admire Your Work
Once cured, remove the item from the oven (carefully!) and let it cool. You'll be left with a beautifully coated piece that’s both eye-catching and protective.
Tips and Tricks
- Grounding Is Key: Ensure a solid ground connection to avoid powder adherence issues.
- Temperature Matters: Different metals will cure at different rates. Keep this in mind to avoid under or over-curing.
- Practice Makes Perfect: Don’t be discouraged by initial mishaps. Each attempt is a learning experience.
The Surprise: Win Your Own Powder Coat Gun!
To those who've made it this far: here's a little incentive. Give this article a thumbs up, drop a comment, and you might just win your very own powder coat gun, courtesy of Eastwood. Check the details below for the giveaway.
Advanced Techniques in Powder Coating
When it comes to powder coating, mastering the basics can lead to exploring more advanced techniques. These methods can enhance the finish, durability, and uniqueness of your projects. Here’s a breakdown of some sophisticated powder coating techniques that can take your work to the next level.
Multiple Coats for Enhanced Durability
Applying multiple layers of powder coating can significantly increase the durability and resistance of the coated item. This is particularly useful for objects that will be exposed to extreme conditions or heavy wear. The process involves:
- Base Coat: Apply the initial layer, which serves as the foundation for additional coats.
- Intermediate Coat: If necessary, apply a second coat for added thickness or to incorporate different colors or effects.
- Top Coat: Apply a final coat, often a clear layer, to protect the underlying coats and add a glossy or matte finish.
Making Special Effects
Special effects in powder coating are achieved by using powders with different properties or by manipulating the application process. Some effects include:
- Textures: From matte and satin to wrinkled or hammered, textures can add a unique touch to the surface.
- Metallics and Pearlescents: These finishes give a shimmering or iridescent effect, mimicking metal or pearl surfaces.
- Translucents and Candies: These semi-transparent powders allow for the creation of depth and vibrant colors when applied over metallic bases.
Utilizing Masking Techniques
Masking allows for the creation of patterns, designs, or areas that remain uncoated. It’s done by applying a heat-resistant tape or silicone plugs to the parts of the object that you don’t want to be coated. After the coating process, the masking materials are removed, revealing the design.
Incorporating Hydrographics
Hydrographics, or water transfer printing, can be combined with powder coating to make intricate designs. This involves:
- Dipping: After the base coat of powder coating, the item is dipped into a water solution with a floating ink pattern.
- Rinsing: The item is rinsed to remove excess ink.
- Top Coat: A clear powder coat is applied to protect the hydrographic design.
Using Infrared Curing
Infrared curing is an advanced technique that uses infrared light to heat the object and cure the powder. This method can be faster than conventional curing and allows for more control over the heating process, which can be beneficial for items with complex shapes or sizes.
Using advanced techniques enhances finishes and meets specific needs. Always prioritize safety and follow the manufacturer’s guidelines when trying new methods.
Troubleshooting Common Issues in Powder Coating
When working with powder coating, you might face some challenges that can affect the quality of your finish. Here’s a helpful guide to identifying and fixing common issues, ensuring a smooth and professional result.
Incomplete or Uneven Coverage
- Symptoms: Parts of the surface lack coating or show uneven layers.
- Solutions: Check your equipment for consistent powder flow. Ensure the object is properly grounded to attract the powder evenly. Apply powder steadily, even strokes, to avoid heavy or light spots.
Bubbling or Blistering
- Symptoms: Small bubbles or blisters appear on the finished surface.
- Solutions: Cure the powder at the recommended temperature and time to prevent overheating. Preheat the object to release trapped gases before applying powder. Inspect the surface for contaminants and clean thoroughly.
Poor Adhesion
- Symptoms: The powder does not stick well to the surface.
- Solutions: Clean the surface to remove oils, dust, or rust. Check the powder’s compatibility with the surface material. Ensure proper curing times and temperatures for optimal adhesion.
Color Variations
- Symptoms: The color is inconsistent across the coated surface.
- Solutions: Use powder from the same batch to avoid variations. Apply a consistent thickness of powder across the surface. Maintain a stable curing environment to ensure even color development.
Fisheyes or Craters
- Symptoms: Small, circular imperfections in the finish.
- Solutions: Clean the surface meticulously to remove all contaminants. Use high-quality powder free of impurities. Apply a thinner layer of powder to prevent pooling and fisheyes.
Careful prep and detail ensure a perfect powder coating.
Maintenance and Care for Powder-Coated Surfaces
Proper maintenance is key to ensuring that powder-coated surfaces remain vibrant and durable over time. Here’s a comprehensive guide on how to care for these surfaces effectively.
Routine Cleaning
Simple Steps for Regular Upkeep:
- Dust Off: Use a soft brush or cloth to remove dust and dirt gently.
- Wash Gently: Clean the surface with a mild detergent and warm water solution. Use a soft cloth or sponge to avoid scratching.
- Rinse Thoroughly: After washing, rinse the surface with clean water to remove any soap residue.
- Dry Completely: Wipe the surface dry with a clean, soft cloth to prevent water spots.
Dealing with Stains and Spills
Prompt Action for Accidental Spills:
- Act Quickly: Clean spills as soon as possible to prevent staining.
- Use Appropriate Cleaners: For tougher stains, use a non-abrasive cleaner that’s suitable for powder-coated surfaces.
- Avoid Harsh Chemicals: Steer clear of solvents, acids, or alkalis, which can damage the coating.
Protecting the Finish
Long-Term Preservation Tips:
- Wax Occasionally: Apply a non-abrasive car wax to protect the finish from the elements.
- Inspect Regularly: Check for chips or scratches periodically. Touch up any damaged areas promptly to prevent corrosion.
- Limit Exposure: If possible, limit prolonged exposure to direct sunlight and harsh weather conditions.
Professional Touch-Ups
When to Seek Expert Help:
- Significant Damage: For large areas of damage or corrosion, consult a professional for a proper touch-up or re-coating.
- Complex Surfaces: If the coated item has intricate designs or hard-to-reach areas, professional services ensure a thorough job.
Follow these guidelines to extend the life and appearance of powder-coated surfaces.
Safety Measures in Powder Coating
Ensuring safety during the powder coating process is crucial for both personal health and environmental protection. Here’s a detailed section on safety measures that adheres to your guidelines for clarity and readability.
Personal Protective Equipment (PPE)
Essential Gear:
- Respirators: Use a proper respirator to avoid inhaling powder particles.
- Gloves: Wear gloves to protect your skin from powder and heat.
- Goggles: Use safety goggles to shield your eyes from airborne particles.
- Protective Clothing: Don a full-body suit or apron to keep powder off your skin and clothes.
Ventilation and Filtration
Breathing Easy:
- Proper Ventilation: Ensure your workspace is well-ventilated to disperse powder particles.
- Filtration Systems: Use a filtration system to capture airborne powder, keeping the air clean.
Fire and Explosion Prevention
Staying Safe from Hazards:
- Grounding Equipment: Ground all equipment to prevent static discharge sparks.
- No Smoking: Enforce a strict no-smoking policy in the powder coating area.
- Fire Extinguishers: Keep fire extinguishers readily available and know how to use them.
Handling and Storage
Safe Practices:
- Proper Storage: Store powder in a cool, dry place away from direct sunlight and heat sources.
- Spill Management: Clean up spills immediately to prevent slips and contamination.
Waste Disposal
Environmental Responsibility:
- Disposal Guidelines: Follow local regulations for the disposal of unused powder and contaminated materials.
- Recycling: Recycle excess powder when possible to minimize waste.
Training and Procedures
Knowledge is Safety:
- Regular Training: Ensure all operators are trained in safe handling and emergency procedures.
- Clear Signage: Post safety instructions and hazard signs around the workspace.
Implementing these safety measures ensures a secure environment for powder coating.
FAQs About Powder Coating
Explore our detailed faqs about powder coating, covering benefits, processes, and more to ensure a flawless finish for your projects.
Powder coating is a finishing process where a dry powder is applied to a surface, typically metal, and then cured under heat to form a hard, protective layer. It works by electrostatically charging the powder particles, which are then sprayed onto the grounded workpiece. The coated item is heated in an oven, causing the powder to melt and form a uniform, durable finish.
Yes, you can powder coat a variety of materials, including metal, glass, wood, and some plastics. The key is that the item can withstand the curing temperature required to melt the powder. Always check the powder manufacturer’s recommendations for compatibility.
Common issues include uneven coverage, bubbles, or poor adhesion. To avoid these:
Ensure the item is clean and properly prepped.
Apply the powder evenly and avoid thick layers.
Cure the item at the correct temperature for the recommended time.
Use a quality powder and equipment.
Powder coating is known for its durability and can last 15-20 years depending on the preparation, material selection, and the conditions under which the coated item is used. It’s important to follow the manufacturer’s guidelines for application and use to ensure maximum longevity.
Absolutely! Powder coating comes in a wide range of colors, and most powders can be pigmented to match nearly any color you need for your project. This allows for great customization and flexibility in design.
Final Thoughts
Wrapping up, this powder coating guide has provided you with essential insights into achieving a long-lasting finish. By following the steps in the powder coating process, you can ensure a durable and visually appealing result. Master these techniques and enjoy the benefits of a high-quality powder coat that stands the test of time.